Synthetic Belts
Our comprehensive range of Synthetic Belts are able to fulfil the application needs for light to heavy processing and conveying applications. Synthetic conveyor belts are made of fabrics with a coating on the top and/or bottom side. A belt consists of one or more fabric plies to give certain features such as strength, stability and impact resistance.
Coating Materials
The coatings used on Synthetic Belts are called polymers and can be made of various materials which have influence on the suitability of the belt in a certain application.
Polymers can be separated into two different groups: thermoplastic or thermoset.
Mainly used compounds for coatings are:
PVC | Polyurethane | Polyolefin | Polyester
PVC
Polyvinyl chloride, commonly abbreviated to PVC, is a widely produced plastic. PVC is a type of thermoplastic polymer that is flexible and durable, and therefore suitable for use on conveyor systems.
Main PVC coating types:
- Flexam
- Nonex
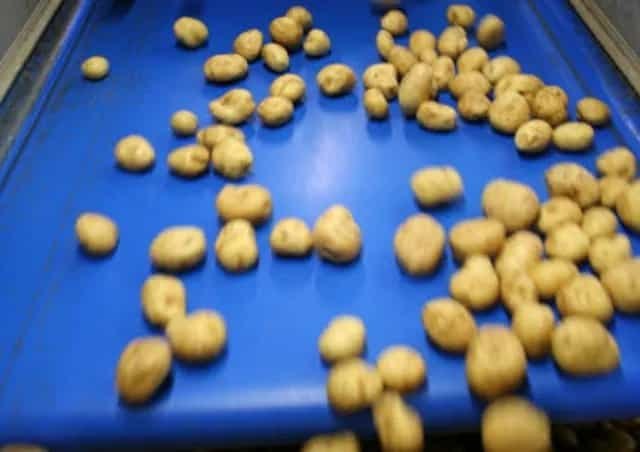
Flexam
Product features:
- Good chemical resistance (including chlorine)
- Hydrolysis resistance (hot water and steam)
- Flame-retardant types available (ISO 340)
- Some food types available (dry food)
- Economically priced
- Available in many different hardnesses, profiles and colours
Industries:
- Airports
- Logistics
- Agriculture
- Fruit and Vegetables
- Marble and Ceramic
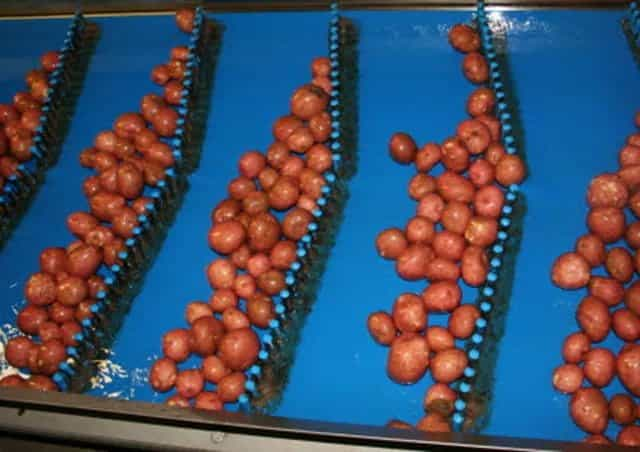
Data Sheet :
- Flexam 514609 (Flexam Putih Profil P41)
- Flexam 573000 (PVC Biru 2mm)
- Flexam 576180 (Sugar Belt 6mm)
- Flexam 579259 (Sugar Belt 5mm)
- Flexam 589539 (Sugar Belt 7.8mm)
- Flexam 589580 (PVC Hijau 5mm )
- Flexam 589600 (PVC Dark Green 3mm Bottom Diamond)
- Flexam 589603 (PVC Hijau 3mm Fabric)
- Flexam 589604 (PVC Dark Green 5,5mm Roughtop A42)
- Flexam 589605 (PVC Hitam 2.5mm Matte)
- Flexam 589606 (PVC Hitam 2,5mm Alur)
- Flexam 589611 (PVC Putih 2mm)
- Flexam 589612 (PVC Dark Green 4mm Bottom Diamond)
- Flexam 589615 (PVC Dark Green 4mm Fabric)
- Flexam 589621 (PVC Tikar P24 S24)
- Flexam 589632 (PVC Hijau 1mm Fabric)
- Flexam 589634 (PVC Hijau Apple 2mm)
Nonex
Product features:
- Good resistance to oil and fat
- Food compliance for all foodstuff
- Available in white and light blue, and with different profiles
Industries:
- Food
- Handling unpacked food
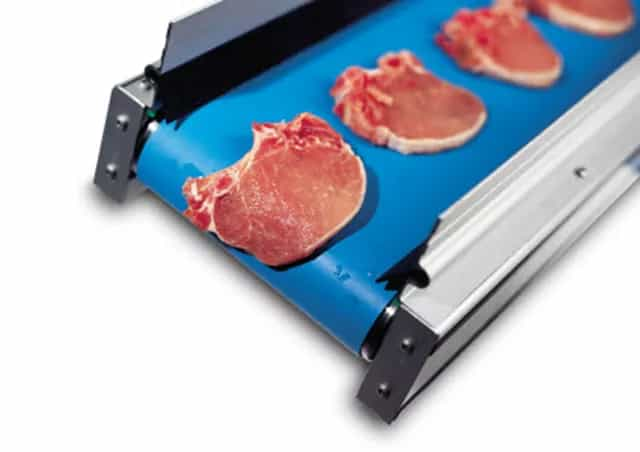
Polyurethane
Polyurethane belts are mainly used in the Food Industry. Due to its structure, polyurethane belts do not give off damaging toxins or chemicals. Polyurethanes for process and conveyor belting can be either thermoplastic – TPU, or thermoset – PUR. Thermoplastic polyurethane coating material excels through its exceptional resistance to grease, oils and chemicals.
Main polyurethane coating types:
- Ropanyl (TPU)
- Ropanol (PUR)
- Ropan (PUR)
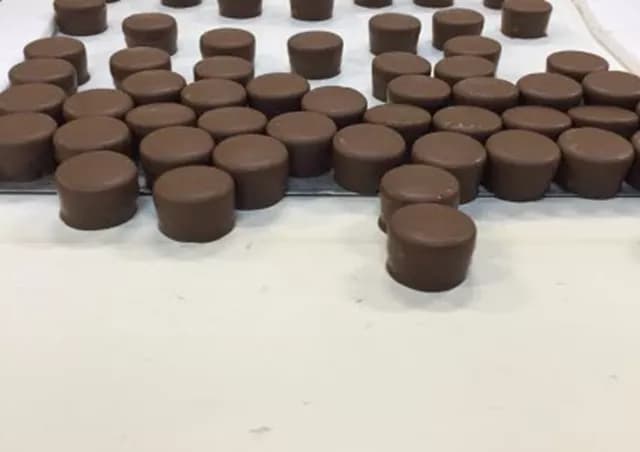
Ropanyl
Product features:
- Belts with thermoplastic polyurethane coating
- Very flexible even at low temperatures
- Very good resistance to oil and fat
- Good abrasion resistance
- Food compliance for all foodstuff
- Available in many colours, and with profiles
- Ropanyl Premium Plus = Non-fray
Industries:
- Food
- Packaging
- Wood
- Good abrasion resistance
- Textile
- Metal
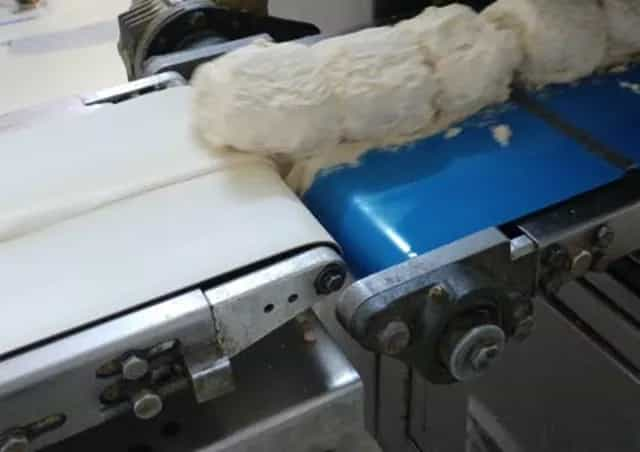
Ropanol
Product features:
- Belts with polyurethane impregnation (zero thickness)
- Low friction top side for accumulation
- Very flexible even at low temperatures
- Good abrasion resistance
- Food compliance for all foodstuff
- Available in different colours
Industries:
- Food
- Logistics
- Airport
- Electronics
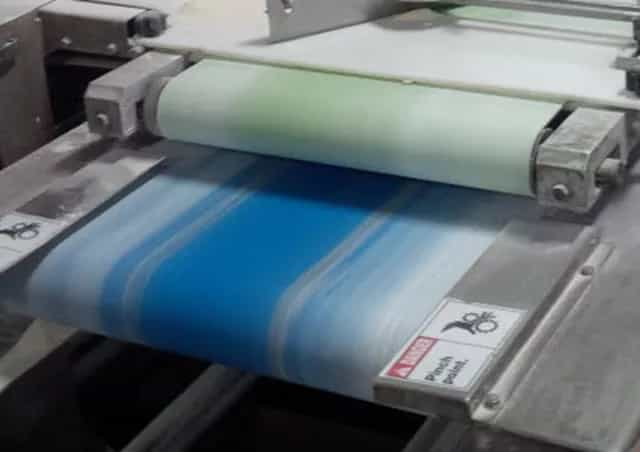
Ropan
Product features:
- Belts with unique heavy duty polyurethane coating
- Extremely good abrasion and cut resistance
- Thermoplastic inner layer, suitable for hot splicing
- Available in white colour
Industries:
- Metal
- Building Materials (bricks)
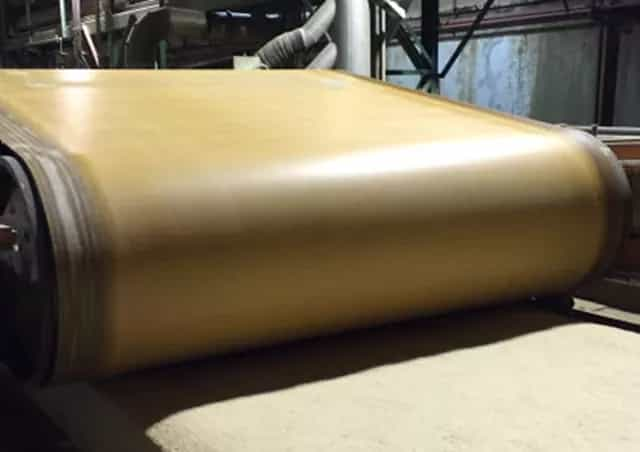
Polyolefin & Polyester
Polyolefins are the largest group of thermoplastics; they are polymers of simple olefins such as ethylene. Polyethylene is probably the polymer you see most in daily life; it is the most popular plastic in the world.
Main polyethylene coating types are:
- Peflex
- Poliflex
- Polikleen
Polyester is a category of polymers that contain the ester functional group in their main chain. Our polyester coating type:
- Amtel
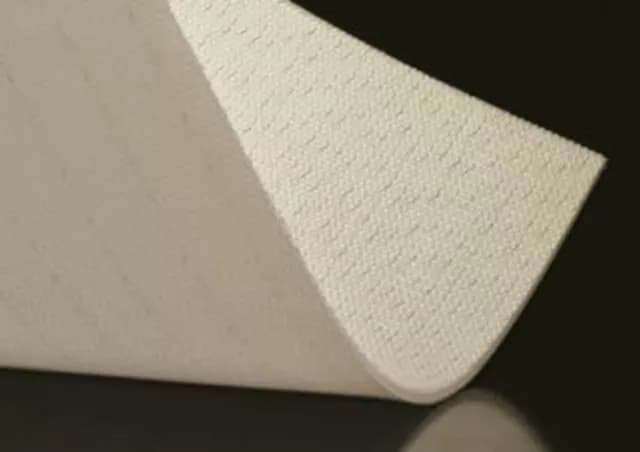
Peflex
Product features:
- Flexible at low temperatures
- Chemically inert material, good chemical resistance
- Pyrolysis resistance (non-toxic when burning, tobacco approved)
- Food compliance
- Easy release properties
- Wide range of types available, with different profiles
Industries:
- Tobacco
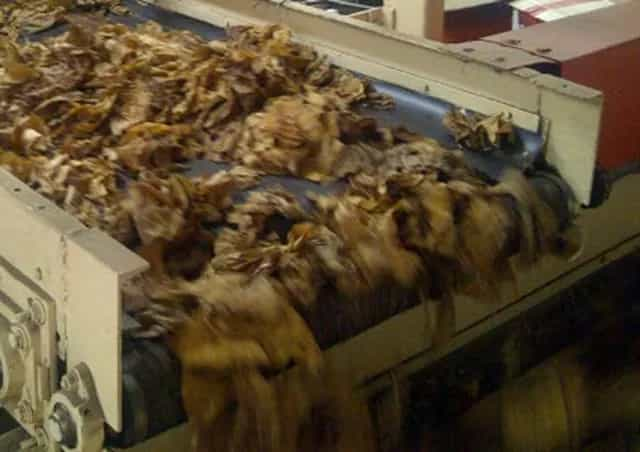
Poliflex
Product features:
- Excellent chemical resistance
- Pyrolysis resistance (non-toxic when burning, tobacco approved)
- Food compliance for all foodstuffs
- Very good release of sticky products
- Special types available for small pulley transfer points
Industries:
- Tobacco
- Food
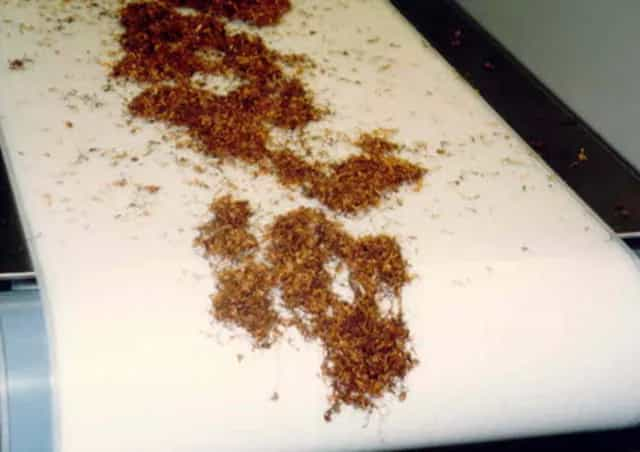
Polikleen
Product features:
- Excellent chemical resistance
- Pyrolysis resistance (non-toxic when burning, tobacco approved)
- Good wear resistance
- Very easy to clean
Industries:
- Tobacco
- Wood (lacquering)
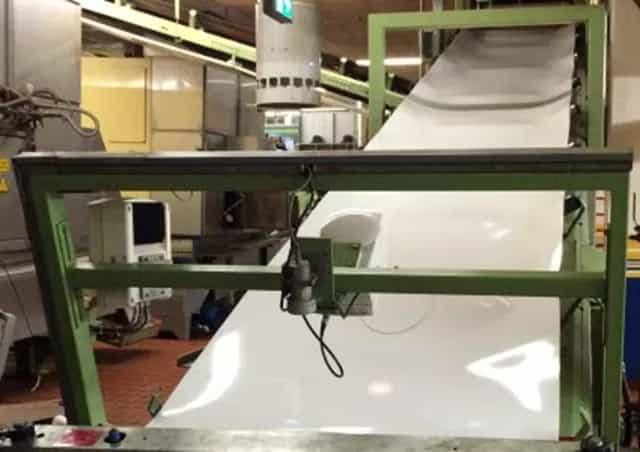
Amtel
Product features:
- Polyester
- Mechanically very strong
- Flexible at low temperatures
- Good hydrolysis resistance
- Pyrolysis resistance (non-toxic when burning, tobacco approved)
- Good abrasion and cut resistance
Industries:
- Tobacco
- Food
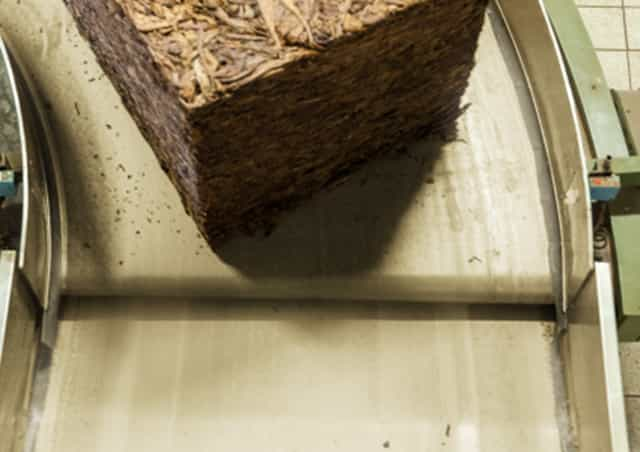
Fabric & Felt
Fabric and Felt belts are used in a wide variety of material transport applications such as car manufacturing, food processing and heavy industry. Felt is a non-woven fabric. The most important raw material for belting fabrics is polyester.
Main fabrics used:
- Cotton (natural)
- Flax (natural)
- Flexible at low temperatures
- Polyamide (synthetic)
- Polyester (synthetic)
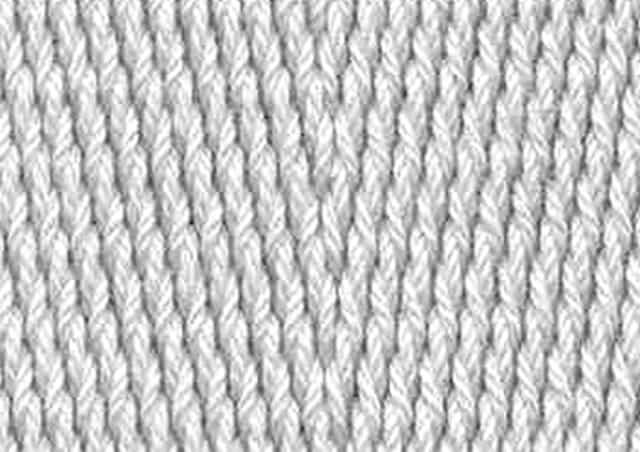
Silam
Product features:
- Good release of sticky products
- High temperature resistance
- Chemical resistance
Industries:
- Food
- Tyre
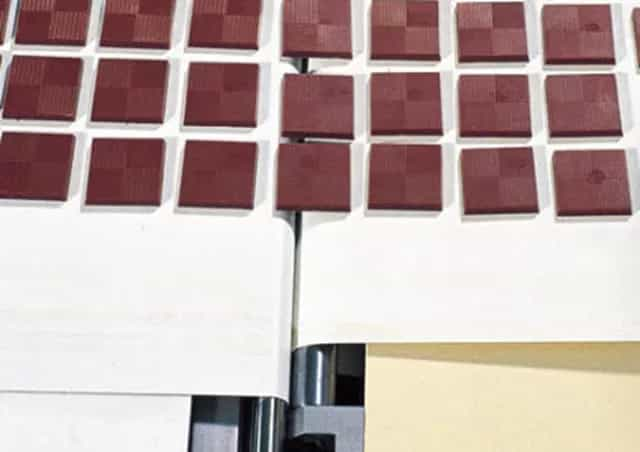
Pletex
Product features:
- High grip
- Good chemical resistance
- Available in red colour
Industries:
- Paper and Print
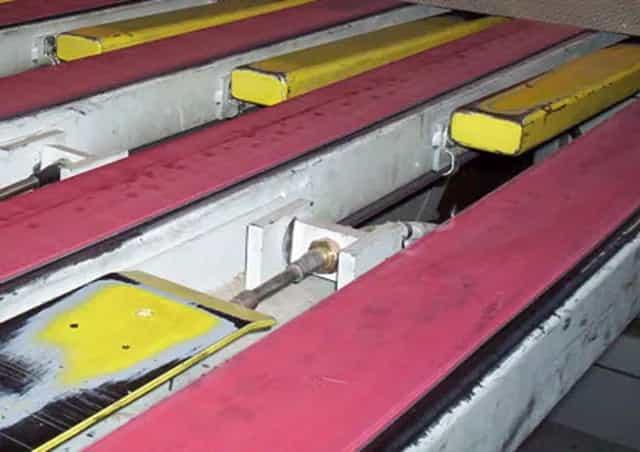
Elastoflex
Product features:
- Very good wear resistance and good grip
- Good oil resistance
- Available in green and beige colour
Industries:
- Paper and Print
- Wood
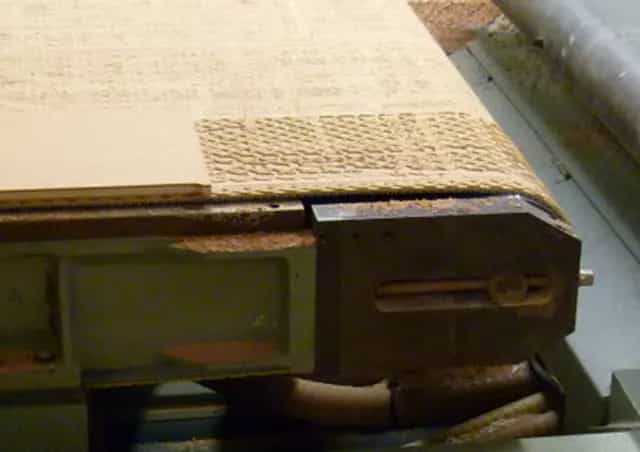
Elastonyl
Product features:
- Excellent wear-resistance and good grip
- Very good oil resistance
- Available in green colour
Industries:
- Paper and Print
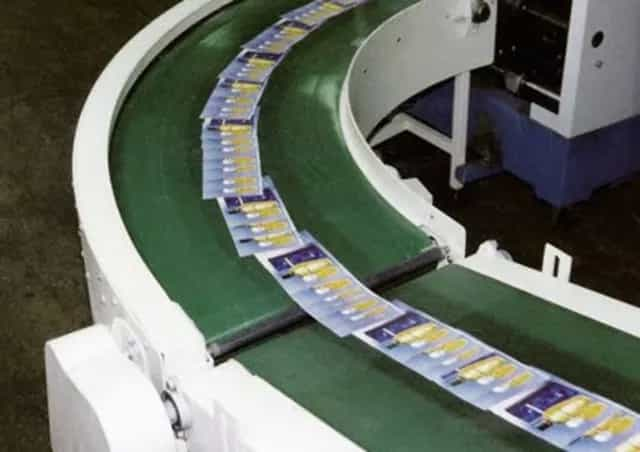
Ultraclean
Product features:
- Excellent release properties
- Very good oil and fat resistance
- High chemical resistance
Industries:
- Food (sticky products)
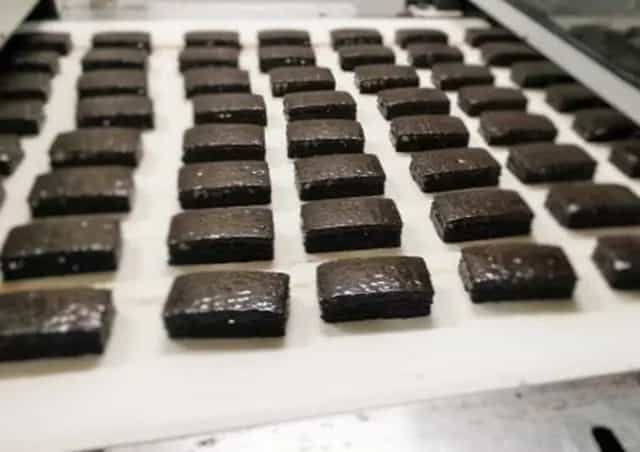
Ultranyl
Product features:
- Very good hydrolysis resistance
- Good oil and fat resistance
- Flexible, suitable for high temperature
Industries:
- Food
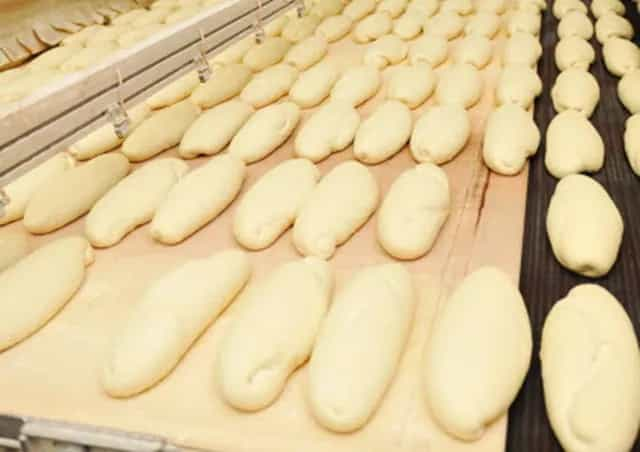
Different Features
Synthetic Belts are produced using different materials, thicknesses, colours etc. Therefore each belt has different features such as high grip, non-fray or wear-resistance for example.
Food Grade belts are primarily used in the Food Industry and the Tobacco Industry. Flame-retardant and energy efficient belts are a sought-after feature in the Airports and Logistics Industries.
Food Grade
For the Food Industry, we manufacture belts for use in high or low temperatures, with excellent resistance to oils and fats and superb release characteristics.
To ensure food safety and to avoid any food contamination, a complete range of belts is available in compliance with:
- the latest EU regulation EC 1935/2004, EU 10/2011 and amendments
- food contact surface FDA standards
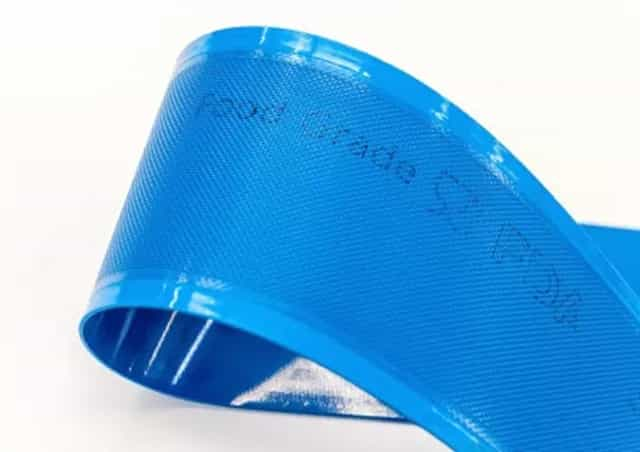
Antimicrobial
Ammeraal Beltech developed belts with antimicrobial additives to assist in reducing the number of microbes on food contact surfaces. This also reduces the risk of food contamination - ensuring optimum adherence to your food safety standards and supports the implementation of your ISO 22000 requirements (previously HACCP).
Our AntiMicrobial (AM) belting range will help to keep the belt cleaner and reduce build-up of bacteria on the belt surface.
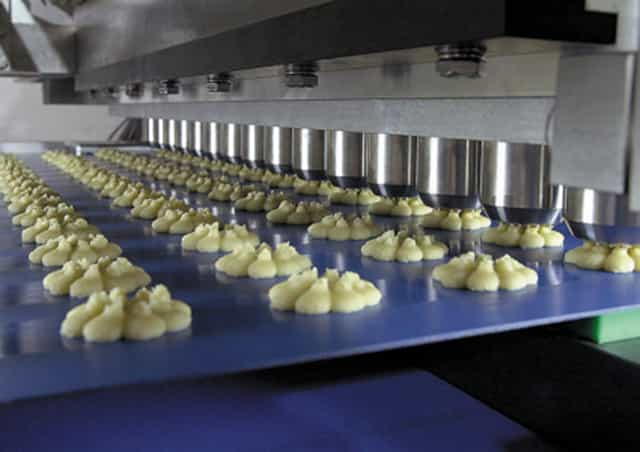
Non-fray
Stronger and tougher than ever.
Our non-fray belts run and remain intact longer and deliver even better food hygiene by reducing fabric fray contamination.
Our KleenEdge and AmSeal Belts tackle contamination risks that may occur from belt edge wear. The belt construction is designed in such a way that the high strength reinforcement fabric is held securely together in a tough non-cracking thermoplastic polyurethane seal.
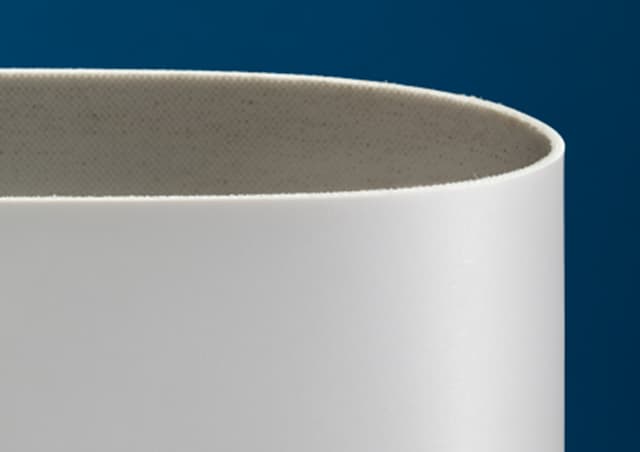
Knife-edge transfer
Particularly when conveying small goods, the transfer between 2 belts must be as short as possible. In this case it is common to use knife-edges.
Knife-edges are used in material handling, primarily on conveyor belts for the Food Industry and for the Beverage Industry. More tension is needed to flex the belt over a knife-edge which causes more wear. This calls for premium quality belts.
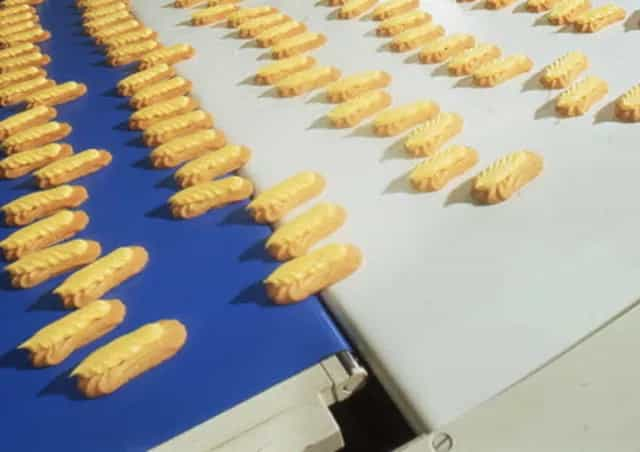
Low Noise, Flame-retardant, Impact Resistant
We offer low noise belts for better working environments capable of high-speed power turns and extremely reliable flame-retardant* belts with extra long-wearing top covers.
Our high impact-resistant belts are able to withstand heavy shock loads.
*ISO340
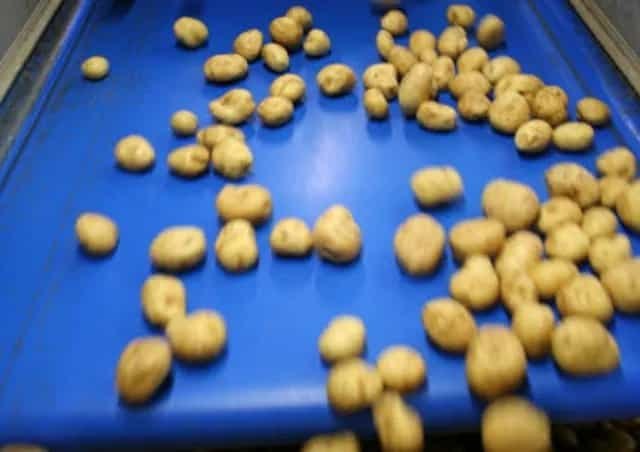
Self-tracking
Working closely with OEMs we have developed a range of self-tracking belts showing superior performance on fixed centre conveyors, two-way running conveyors and wide, short centre belts. Tracking of a belt in these situations is always very difficult.
- Reduced maintenance costs
- Compact conveyor design
- Less energy consumption
- Easy and quick installation
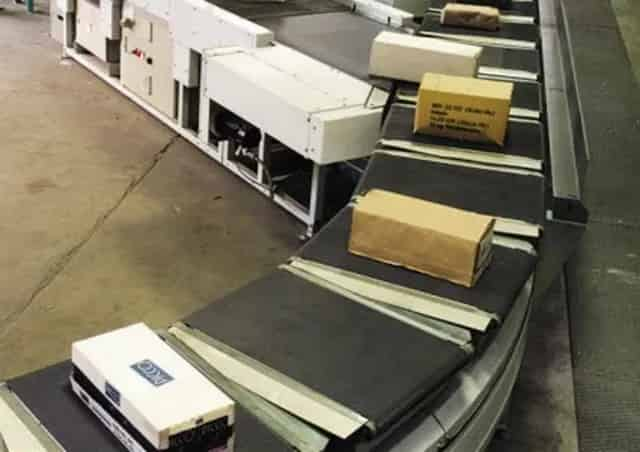
High grip
Our high grip belts are specifically designed to increase the friction between the belt and the products being carried. This is often needed for inclined transport or in slippery conditions.
High grip characteristics can be obtained by using different materials and/or using certain profiles (embossing).
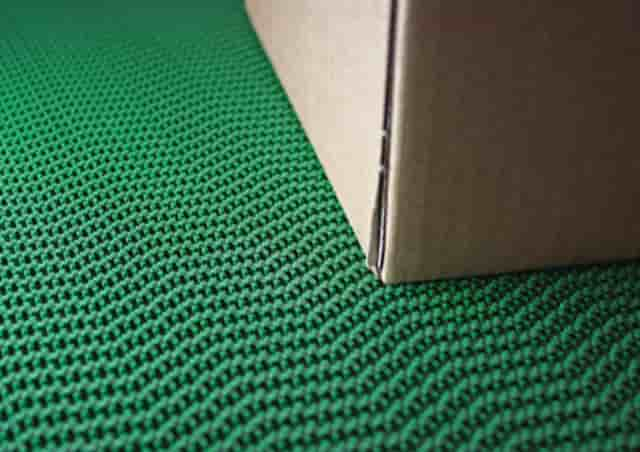
Wear-resistant
We offer a range of wear-resistant belts that are specifically designed to handle even the toughest conditions you can think of.
Wear-resistance is one of the most important properties that determine the life expectancy of a conveyor belt.
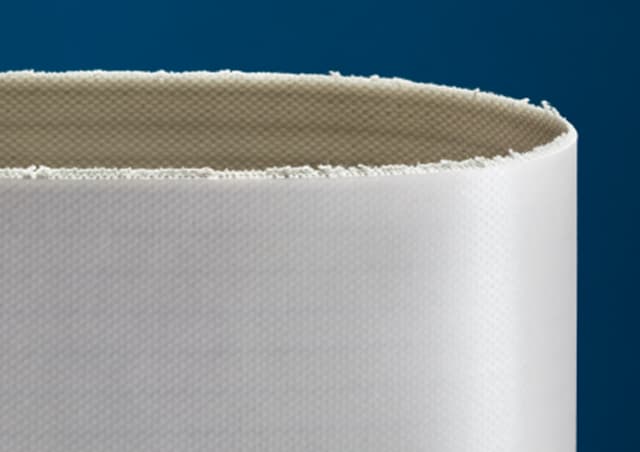
Energy saving
To ensure that belts run as efficiently as possible on conveyor systems, we present a series of belts that offer the potential of a considerable power consumption reduction.
Belt selection is a very important factor in saving energy, but not the only one.
Ammeraal Beltech’s ‘Energy Saving Concept’ is based on 3 pillars that influence the power demands of a conveyor:
- Conveyor design – in order to get the basics right
- Belt selection – in other words, a fit for purpose belt
- Drum motor sizing – not too big (wastes energy) and not too small (will be overworked)
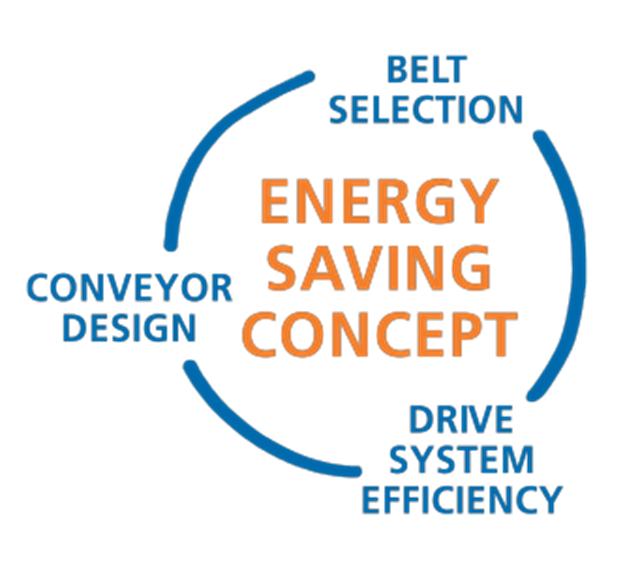